To function during flight a sub-orbital rocket needs a service system in order to do science and send sensor data back to the ground. The engineering department at Andøya Space have developed a new service system that can transmit three times more data than the previous system.
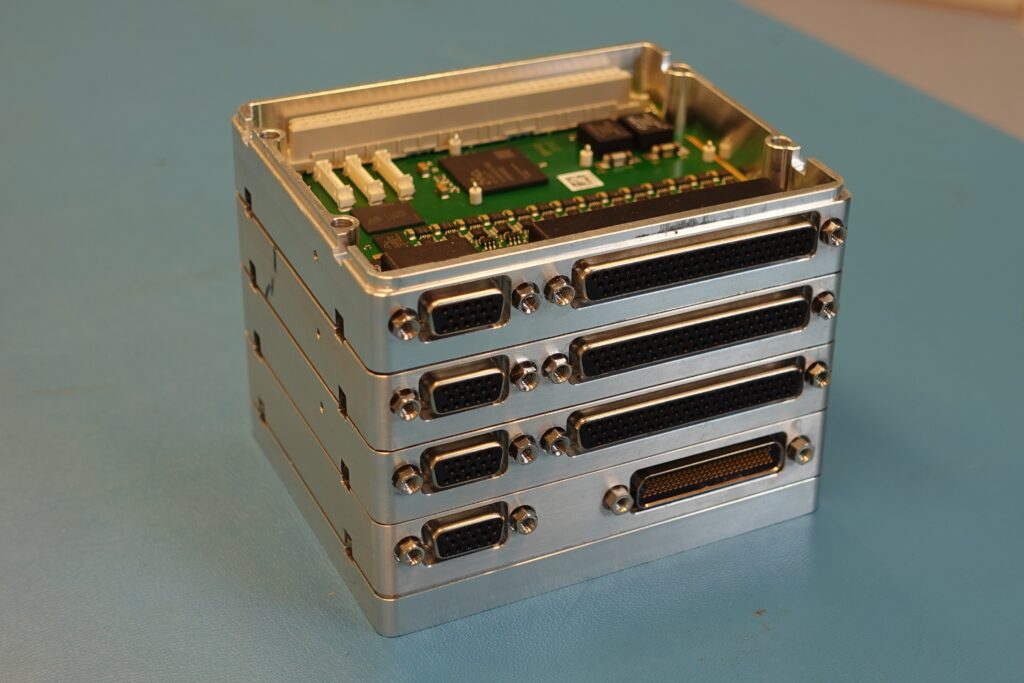
– A service system is essentially a support system for the rocket payload and the onboard instruments. It has several tasks, but it basically comes down to getting the instruments into the right position to do science and send sensor data back to the ground, says Aerospace Chief Engineer Geir Lindahl at Andøya Space.
He is one of the engineers who have worked closely with the development of the new system.
The service system is composed of four circuit boards, stacked on top of each other and mounted in an aluminum casing of approximately ten cubic decimeters, which is approximate one liter. These circuit boards handle four sub-tasks: data-encoding, data acquisition, power management, and event-handling.
Data encoding is the process of collecting data from several different sources, sorting it and translating it into a bit-stream of zeros and ones.
More than just an encoder
– This is often thought of as the main task of the service system, and therefore the system is often mistakenly said to be an encoder. It is an encoder, but it is so much more than that. The encoder is only one fourth of the system, says Lindahl.
The power management system delivers power to all systems and controls the switching between battery and ground power. The event handler is detecting lift-off and arms the onboard pyrotechnics.
During a flight the payload often separates from the motor, opens hatches, releases the nosecone and deploys a parachute. All these events are controlled by the event handler. The data acquisition system allows analog sensors to be interfaced directly to the service system.
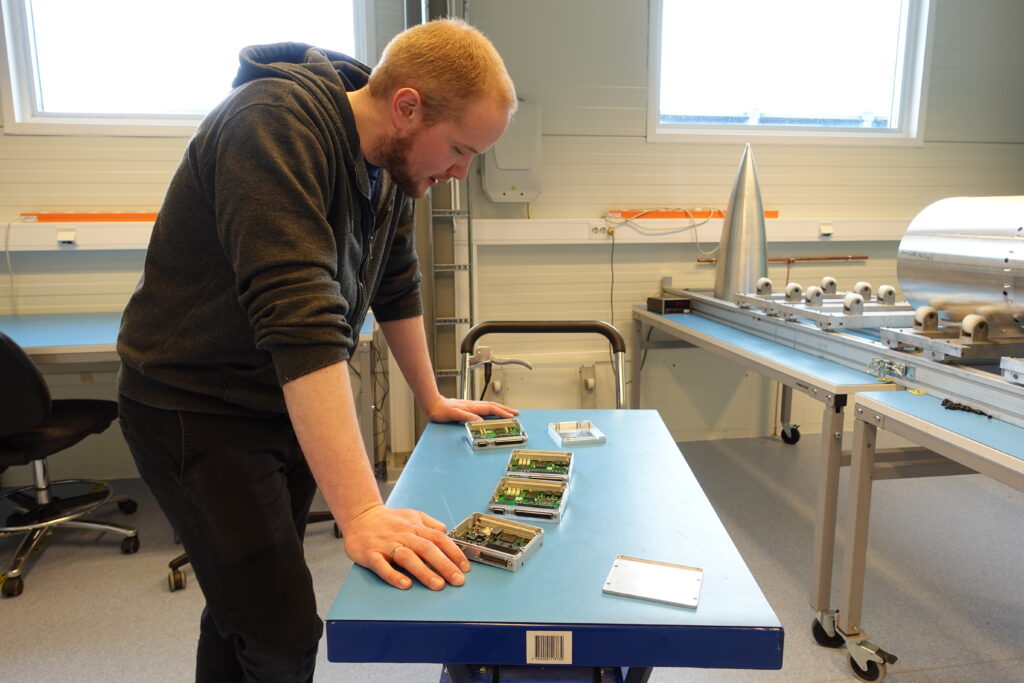
Improved capabilities, three times more data
The new service system will be transmitting three times more data compared to the previous system. The data acquisition has 16 times better resolution. This allows for higher resolution and more detailed analysis on a finer scale.
– The system has also been extended to comply with more digital protocols making it easier for the customer to interface, says Lindahl.
A sounding rocket can travel up to a couple of thousand meters per second. To do fine scale measurements at this speed, a high sampling rate and high data throughput is essential.
The first launch to use the new system will be the Norwegian sounding rocket Maxidusty 2, scheduled to be launched in the summer of 2024.
A challenging project
Andøya Space has been building payloads for over two decades, and all payloads require a service system. Earlier flights used the predecessor, STAPPE 1, which was developed by the Norwegian Defence Research Establishment (FFI).
However, when FFI ended its sounding rocket research, the design wasn’t renewed. Components became obsolete and it became impossible to produce more units of the old system.
– We didn’t have much experience with designing service systems to start with, so the learning curve was steep. Luckily, we had FFI to lead the design and help us, says Lindahl.
In the middle of the project, Covid-19 happened. This had a large effect on the production of electronic components and caused a global component crisis still felt today.
– Some components were almost impossible to get hold of with lead times of up to several years. As a result, we had to redesign and change part of the original design, which increased both development time and the cost , Lindahl says.
Ready for launch
– The service system has gone through all bench tests with flying colors and is now ready to be tested and used together with the scientific instruments before launch to see how well our system performs together with other systems, says Lindahl.
He is very pleased that the new service system is now completed and ready to be used for launches at Andøya.
– It feels great that this long project is finally finished. It has been a good learning experience and we have gained a lot from FFI’s extensive knowledge. I feel like the torch has been passed to us in a good way. We own the design and have the knowledge to develop the system further ourselves. We are very happy to present the new system to our customers, Lindahl concludes.